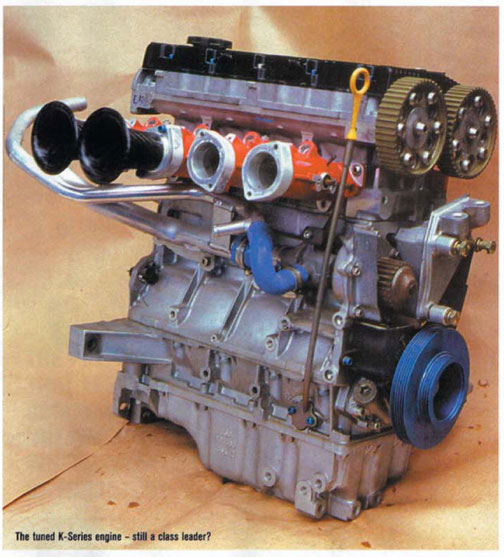
KING K
Simon Erland
revised 12/04
(The opinions expressed in this article are not necessarily those of the author of this website. Care must be taken when making any modifications to an automobile and results may not be necessarily forthcoming.)
History of Problems
Rover's K Series: a lightweight, technically advanced easily tuneable four, or an unreliable and fragile lump?
Three years ago, I bought from the Commercial Director of the Lotus One Make motor sport aseries my Lotus ex-racer. Dave Cooling had recently left Lotus to pursue his own business, but was and remains very close to the company. It was on the drive to the factory, where I had been invited to meet some of the Lotus engineers, that Dave regaled me with stories of how much trouble they had had with the K Series engine " with vibration, with bottom end failure and endless blown gaskets. He revealed that they had thought very hard about junking the K and replacing it with the Honda S2000"s 2litre engine, which as Dave said, would give a "reliable" 237 bhp.
On arrival I was met by Myles Lubbock, chief engineer on the One Make Series and his right hand man John Danby, both of whom knew that I had done a lot of work on the K Series engine in pursuit of a bullet proof 350 bhp supercharged engine. It was immediately clear from the moment that I met them, that they were having all sorts of problems with the One Make race series engines. In fact, they were at their wits ends and had very little respect for the engine. Myles, a serious and able engineer, told me of their problems and efforts to understand them, of even doing a tranche of tests with vibration sensors mounted all over the block to measure what he considered to be the engine"s weakest feature. His assertion was that the engine was made out of very poor quality metal and the block suffered from enormous distortion. He thought the engine fragile, and I suspect more trouble than it could possibly be worth. They were also having immense problems with gasket failure, and even as recently as November 2002 when I spoke to Tony Schute, head of the Elise development program at Lotus, it was plain that Lotus had an engrained belief that the K would suffer gasket failure in any engine over and above the 190PS VHPD specification within an unreasonably short period of time.
Lotus are not the only people familiar to this experience. Another car manufacturer specialising in road/track day racers produced a flagship model a couple of years ago boasting trick throttle bodies, a steel bottom end and 230 bhp / 9200 rpm specification. Caterham"s R500 is a stormer, regaled as being quicker in a straight line than the McLaren F1, but has gained just as vivid a reputation for fragility, notably for putting rods through the block. I myself have met five owners of cars whose engines have done just that, Dave Andrews tells me of more, and all the journalists from the mainstream motoring magazines relate stories of great car " until the engine goes. Similarly, there are engine builders up and down the country who look upon the K as all too breakable in their experience, and the letters pages of the motor sport press have, in their time, been full of stories of cracked liners, blown gaskets, spun bearings, and in fact all manner of woe.
Is the K Series really so poor? And if so, why are some of the leading sports car manufacturers using it? I firmly believe not and rather that it is in many ways the best four cylinder engine around despite its age. During the last three years, I have done a great deal of research into the engine and particularly bottom end loading, in which period I have been lucky enough to be able to call upon the advice and opinion " sometimes very colourful, of the design engineers for K at Powertrain Ltd " MG Rover Engines. In this time it has become very evident that the engine is very sound, its basic design having had just two minor flaws both now remedied, and that the problems that have beset K, are entirely due to poor quality aftermarket components and bad engine building by many of those tuning the engine " people are building problems into K!
Basic Design
It is useful firstly to look at the basic construction and compare it with other four cylinder engines around at the moment. The brief for K was originally for 3 and 4 cylinder aluminium engines that would be both lightweight and efficient to power a concept car called the ECV3, then under development at Rover"s secret Gaydon research centre. Conceived by Spen King, ECV3 was the first bonded all aluminium chassis and the original K engined prototype that proved the technology that Lotus later adopted for the Elise. Few people realize that this revolutionary concept was not only a Rover project but was also conceived with the K series engine as integral to the project. The 3 cylinder was dropped and the K eventually emerged in 1.1 and 1.4 litre, single and DOHC forms. The original engine had a top hung wet liner, now replaced across the 1.4 " 1.8L range with a floating half-wet liner. The block on the early 1.4 was closed at the top, and this has sponsored one of the many myths about the K, that the early 1.4 is a stiffer and better block. Some engine tuners look at the current block with its fully floating liner and immediately cry out in horror. I haven"t, prior to publication, managed to elicit from Rover precise figures for torsional stiffness for the two blocks. However, the engineers are quite clear " the blocks do have slightly different figures for stiffness, but the later block was designed to be as stiff in every required axis as the earlier block. There is absolutely no problem with this design. Indeed, it does make me wonder about the experience of some criticising this block design when it is quite common for the top half of the liner to be laterally unsupported in V8 engines. For example, the current Indy engines use exactly this design and no one would think to criticise them for this concept. It was also this that allowed the bore to be stretched to 80mm on production engines and subsequently 82.5mm for the new generation of 2.0L engines. An 80mm bore 1.6 litre was in fact extensively tested as a wet liner in the early closed block but the liners tended to crack " this occurs with iron liners because of loads imposed through the block acting as a moment at the top of the liner, though this happed at the very high mileage cycles that road engines are tested at. By making the liner a fully floating design, these stresses cannot act at the top of the liner and then cheap spun iron liners become viable, otherwise steel liners which exhibit at least three times the hoop strength are required. This problem was encountered with the "common" BMW engine with a closed block which MG Rover design engineers worked on to eventually consolidate 4 cylinder engine production in the BMW days. The fully floating design is a clever and effective solution seen in many engines, not least the newest generation of Honda and Toyota engines and there were absolutely no compromise in the stiffness of the second generation K series block.
The block and ladder frame that support the crank were an absolute first for a mass produced engine. This arrangement is immensely stiffer than conventional bearing caps, which allowed the block to be very light. This is the area of the block that actually supports the crank and therefore carries all the loading imposed on the engine by the crank. It is where stiffness is actually required in an engine. This design was only previously seen in fully-fledged race engines " F1, Nascar, etc. and had never before been seen in a 4 cylinder. It is one of the design elements that make the K such a sophisticated and efficient design. Far more so than, for instance, all current Ford 4 cylinders including the Yamaha/Ford 1.7L in the Puma and the very new all-aluminium 2.0L Duratec, plus the likes of the much vaunted Honda 1.8 VTEC. The only engines which have caught up with the K are the 2.0L in the Honda S2000, the 2.0L from the Civic-R and the 1.9 VVTi in the Toyota Celica. All are copies of the K Series in this essential area of engine design.
Another frequently heard criticism of the K that it has very narrow main and big end bearings. This is a feature of the fact that the engine is very compact with narrow centres of 88mm. Only the Yamaha/Ford Puma engine at 86.5mm and the Yamaha/Toyota VVTi at 87.5 are narrower. This again contributes to a lightweight block, but I would say to those who consider that the resultant narrow bearings are a weakness, to look at any of the current F1 engines. Having seen a stripped down 1997 Supertec engine I can tell you that the F1 engine bearings are not huge and like the K"s, are certainly a lot narrower than the older generation of much tuned Ford engines or any of the new generation of in line 4"s, with the exception of the Puma and Toyota engines with their bike heritage. There are good reasons for this, firstly narrow big end journals with slightly larger diameters give good bearing overlap which makes for strong cranks and secondly the larger the bearing surface area the greater the friction loss in an engine. Therefore, it is in the interest of power output to have as small a bearing as possible. In order to enable this, the loading on the bearings needs to be minimised. This in turn is achieved by having as stiff a crank as possible, by accurate counter weighting in the crank and careful associated design of the block, by having as low a reciprocating mass as possible and specifying a tight F3 dynamic loading tolerance. It is worth noting that the K"s tolerance for the latter is half that for the Ford, Alpha and Mercedes engines I have tolerances for, and for that reason the K is a well balanced engine with low resultant F3 bearing loads. Most Ford engines are particularly poor in this respect.
Loads imposed on the block by the rotating mass and fluid forces " combustion loading, will cause any engine to flex whether it is an old iron dinosaur, such as a Chevrolet V8 or Ford Zetec, or the modern aluminium block in a Puma, or the K. The problem is to manage these stresses. The K does this by, instead of using a series of bolts to close the cam carriers-to-head and head-to-block and block-to-ladder, one long bolt which goes right the way through the engine. The metallurgy of this bolt has been very carefully designed and the torqueing at 64Nm brings the bolt to its yield point. Effectively the point at which the bolt will stretch with the block under its cyclic loading, to distribute these loads very evenly throughout the block. Thus the block is relatively unstressed within the design parameters for performance for the engine, the load being carried substantially by the long bolts. This also contributes to reducing the mass of the block. The design and metallurgy of these bolts is critical to the whole design and loading that the engine sees, which has, as we shall see, has implications for some of the aftermarket tuning going on with non OE bolts.
Engine Weight Comparisons
All of this tends towards an engine that weighs in, as standard, fully dressed at 96.5 kg. Compare this to the Honda S2000 engine similarly equipped with standard manifold clutch and fluids at 158 kg and the Toyota 1.9 VVTi engine at 137 kg. The Rover engine"s compact size and weight are a significant advantage in a lightweight race/sports car of the Lotus 7 type or the Elise. Note, a full race K Series weighs 78 kg including 7 kg of fluids. Compare these figures for output in terms of power to engine weight. See Table 1.
Engine |
Power Output |
Power / Engine Weight |
Ford Duratec 2.0L |
140 bhp @ 6000 rpm |
1.16 bhp/kg |
However, this tells only part of the story because most of the Japanese engines like the old 1.8 VTEC and the new I VTEC engines are all short stroke, big bore engines, all of which have a relatively narrow power band. The K with its 89.3 mm stroke produces a lot more torque and spread over a wider engine speed range. This makes the K"s power to weight ratio all the more remarkable in the context of lightweight sports/race cars, and given its more advanced construction than all but 2 or 3 of its most recent competitors, it is clear that the K has a very strong claim to be the best 4 cylinder engine around. In fact, given the huge weight penalties of the Japanese engines and the backward design of the new 2.0L Ford " indeed most of the engines around at the moment, the only clear competitors to the K"s crown are the motorcycle derived engines.
The limitation of any normally aspirated engine, that is an engine that is using engine speed to pull the fuel mix into the cylinders and hence produce power, is piston speed. Piston speed is a function of both engine speed and stroke. To put the K"s ability into perspective the Honda S2000"s 2.0 litre engine the one that the Lotus people on the one make series aspired to, revs to 9000 rpm as a production engine. With an 84 mm stroke this achieves a piston speed of 4960ft/min, with its longer stroke the K achieves this at 8460 rpm, something the standard K bottom end is perfectly capable of, with the sole modification of forged pistons. The R500 engine achieves a piston speed of 5390 ft/min at 9200 rpm [ the R500"s rev limit has of late been cut to 8500rpm, in an attempt to stem the failures of this engine], a figure that the Honda engine would only match were it to be revved to 9,800 rpm. The point is that big bore short stroke engines are conceived to make high engine speeds possible, the penalty is poor torque, the Honda 2.0 litre S2000 producing just 151 lb/ft @ 7500 rpm, a figure easily eclipsed by the 1.8 litre K equipped with Piper"s 1227 cams which will give a very similar power output to the Honda engine. So, the Honda is not such a special engine. It does have a very strong and stiff block, being a copy of the K Series" design, but suffers from its enormous weight of 158 kg in standard form fully dressed (figures from the Vemac Car Co.) more than 60 kg heavier than the standard K. The only really attractive part of the Honda"s design are the roller cams which do reduce friction in the valve train but in every other respect the K is a more efficient and effective design than the Honda.
All this of course is on the assumption that the K can do this reliably, and the truth is that not only is there a perception of a fragile engine but there have been an enormous number of problems, from gasket and liner failure to complete catastrophe with the bottom end and on everything from the numerous privately modified engines, to the flagship models of commercial sports car manufacturers.
So what is going on here? Well, there are myriad of hysterical myths and oldwives tales told about the K, but there is also some kitchen sink engineering being done by the tuning companies. The only way to put this straight is to look at the engine, element by element.
Fixing the Problems
As a 1.8 litre there are, or were, two minor problems, design features of the basic engine which did give rise to problems when the engine was tuned. The first is the positioning of the thermostat in the cooling system, which was not designed for engines frequently put under heavy load. It was first designed as an efficient engine for lightweight front wheel drive cars, typically the Rover Metro and the current Rover 25, with good fuel consumption and requiring low emissions from start-up when the car was likely to see a large number of very short inner city journeys. It was thus designed to give very rapid warm up by placing the thermostat at the coolant inlet to the engine, where the thermostat measures essentially cooled water from the radiator with a very small quantity of heated water from the balancing circuit until the stat opens. This is a very unusual coolant path design, but is effective in its required purpose.
The system does not function well in cooling circuits with a radiator a long way from the engine in the cooling path, or for engines constantly seeing high engine speeds .The problem arises when the engine is put under heavy load, causing high engine temperatures that are not immediately read by the thermostat because cold water in the radiator and hoses has to pass the thermostat first. This can cause enormous thermal gradients across the engine, causing both distortion of the head and block and also gasket failure. The vehicle which suffered most from this was the Land Rover Freelander. Apparently, the typical owner for this vehicle is the middle class housewife and mother who use it for large numbers of short shopping trips to the supermarket!! Being heavy and 4x4, the 1.8 litre K"s tend to be pushed very hard from cold. This results in the engine getting very hot before the water can circulate and open the thermostat. Result " blown gasket. Early last year, Rover introduced a new thermostat, the PRT thermostat that will open with pressure as well as temperature, the result is that it opens much more quickly and prevents this thermal shock across the engine. There still appear to be problems with the Freelander, amid concerns that Ford have already executed a cost down on this new thermostat. However, it is quite apparent that as soon as the thermostat is moved to the output on the engine that temperature related gasket failure no longer becomes an issue. It is something of a surprise therefore that the Ford engineers concerned with the installation and performance of the K in the Freelander do not adopt this simple approach. The PRT thermostat is also a very expensive item that must be an issue with such pressure for cost downs. However effective the PRT thermostat is for a road car, a far more effective solution for any engine used on the track, and in fact any Elise with its problematic long coolant hose runs is to move the thermostat to the output side of the engine. Both Elise Parts.com and QED do inexpensive remote thermostat housings for this purpose. When one of these units is employed, the thermostat is measuring the engine temperature and is therefore able to control the coolant temperature quickly and sensitively.
Removing the thermostat altogether, as currently practiced by some, is no solution, firstly because engine warm-up becomes protracted, with all the implications for premature engine wear and secondly, because the engine temperature is at the mercy of the pump speed, if engine speed falls, the coolant in the radiator will cool disproportionately, then as soon as engine speed builds and engine temperature with it, the pump speeds to sends a mass of very cold water from the radiator suddenly to the engine. There is no thermostat to even this process out so the engine is repeatedly subjected to thermal shock. Bad for the head, bad for the block, and sooner or later the gasket will go. Fit the thermostat to the coolant output and the extreme temperature gradients that beset the engine when used on the track are significantly mitigated. Modification of this coolant path is something that Lotus should have done with all the K series engines in all their Elise"s, This would have then prevented any gasket failures.
Stress Relief
Whenever a block is cast, whether it is lightweight aluminium, or an old fashioned iron block, the casting process followed by the quench sets, up enormous stresses within the block. In a normal production process these are ignored and the block is machined for use. These remaining stresses will always work their way out of any block as it is subjected to thermal cycling. Consequently any serious engine builder will always prefer an old well used block that has seen many thermal cycles because it is only at this point that the block becomes dimensionally stable. Of course once this state has been achieved all the machined surfaces are out of true and the block will require re-machining, this is always desirable as part of the blueprinting process of a thorough engine build. In a production engine , excessive thermal cycling is therefore a disadvantage because it will see a block go out of true and the more severe this cycling is, the more deformed the dimensioning becomes. This is a particular problem for the K series as a lightweight block and can cause liners to sink on their shoulders, giving effectively an uneven deck height. Since the block will always expand at least 2thou more than the iron liners at working temperature, liner stand-proud will become a potential cause of gasket failure. If the stand-proud varies from cylinder to cylinder or is less than 4thou, gaskets in engines with high cylinder pressures, particularly the VHPD are prone to failure. The tolerance for standard factory Ks is set at 0-4 thou and standard engines, provided they are not thermally stressed seem to work well enough with this tolerance. Since 2003 the liner specification has been modified and all engines now have a 4-5 thou tolerance set for liner stand proud. Modification of this tolerance and the thermostat location in the coolant path is an absolute essential on any K series engine used on track.
To digress for a moment, the other engine component carried over by Lotus that makes little sense to me is the right-hand side engine mount. This huge rubber bush, called the hydro mount was a replacement for an earlier simpler smaller bush in the front wheel cars, to make Rover saloons more refined. It is surprising to see it carried over to the MGF. Frankly, it is bizarre to use it in the Lotus. The bush is so floppy that it allows a truly massive amount of engine movement in the chassis. This undoubtedly hurts traction, but worse, causes huge weight transfer when cornering. The last thing anyone wants in a race car and I am sure this contributes to the sudden over-steer that the Elise suffers from. Replacing this mount with the original Rover 200 mount not only stiffens the engine mountings but saves a lot of space and weight!
Dowels
The second problem with the engine has also now been resolved, but was partly responsible for creating some of the myths about the integrity of the block and liners. The K Series was designed and originally manufactured with steel dowels, to locate the head to the block. Unfortunately, these were replaced with plastic dowels in early 1.8 engines which were also used in most of the VHPDs. This was a mistake and the dowels were re-specified as steel in 2000. All replacement gaskets now come with replacement steel dowels to retrofit to the entire K series family.
The problem with these plastic dowels was that they were not such a problem, not in Rover"s own cars at any rate, in the same way that the thermostat could be however in engines that were regularly revved hard and to the rev limit, head shuffle became a problem. There was clear evidence on the engine from my Lotus of relative movement between head and block when I stripped the engine down. The plastic dowels were nearly severed and the long bolts exhibited clear witness marks at the point where the holes in the head for these bolts open up to become an oil way. This problem effectively solved with Rover"s own steel dowels and together with the new PRT thermostat, eliminates the only two significant problems with the basic engine.
The plastic dowels have had one unfortunate consequence in misleading many into thinking that there is a problem with the liners themselves. The liners are in fact totally sound and quite capable of coping with the cylinder pressures associated with the clutch of 250-255 bhp normally aspirated engines around. On only one of these engines so specified, Jason Krebbs" Caterham, have I found a failure and that because one of the drivers on a track day test for a magazine managed to buzz the engine to 16,000 rpm " recorded on the data logger, causing just one liner to split. Apart from that, I have not managed to identify any substantial problems with the standard liner apart from a small batch of liners supplied by their manufacturer GKN, which suffered from some porosity. These were quickly identified and eliminated by Rover many years ago.
Head shuffle became a problem with the engine still equipped with plastic dowels. This can allow the liner to rock in the block, come away from the fire ring, and eventually split. This was often seen on the earlier engines when pushed hard, but not ever on engines equipped with the steel dowels. It is however the cause of the myth about weak liners in the K. Anyone who has an engine with the plastic dowels which must be most of the unmodified Elise"s, should take the opportunity to fit a properly ported head, the steel dowels that come with the new gasket and can then have absolute confidence in the liners.
Liners
Liner failure on many of the early tuned Ks was common, but few thought to question the plastic dowels and instead tried to find solutions by modifying the liners. This brought about many bizarre and totally unnecessary "would be" solutions. These included liners soldered together to form a mono block, banded steel liners and blocks with the tops welded in to form a closed block. All of these came about as solutions to a problem that was totally misunderstood and is an example of the lack of thought and systematic effort in handling this engine. A clear example of which is the example of Scholar"s EVO4 block. Alan tells me he has never himself built an engine that has failed with standard Rover liners, but was told that his predecessor building the One Make series engines had suffered many failed liners. In fact Minister had built all the first season"s engines with plastic dowels " the EVO4 block was just a leap into the dark. In fact closing the top of the block will succeed only in interfering with the engine"s cooling. It is where the modern generation of engines have gained efficiency and so output. All the most recent Japanese engines are open topped and are in fact copies of the K, the only distinction with the Japanese engines being that they have cast in liners, which makes the liners very expensive to upgrade. In addition, welding in a great deal of new metal will cause the block to distort and so will cause the block to have to be re-machined. This is fine provided the boring and milling machines are at least of comparable standard to the factory machines. I have my doubts about this, in the same way that many of the aftermarket companies are using inadequate balancing machines and I have seen several heads that have been skimmed on mills where the bed is not plane parallel to the cutter. I have no doubt there are equally inadequate boring machines out there. All this when it was only the plastic dowels that were at fault!
If the liners are totally sound, they are not without disadvantages. Chief is that the fit of the early liners into the bores was poor, causing a great deal of liner movement and with the high rod angle of the 1.8, that caused significant piston skirt to liner friction. This is always evident on the bruised skirt from 1.8 pistons and therefore as a matter of efficiency, if not reliability, the liners , are better replaced by the Chromoduro liners which are not only made in steel and have the low friction lubrichrom coating but are toleranced to not move around in the bores and give the ideal 5thou stand-proud. Last year the standard Rover liners were re-specified, for much better fit to the block and stand-proud. The tolerance on bore was also tightened, so now there is only one liner grade, similarly with the pistons, no longer are there grades A and B. A second disadvantage is that cast iron liners will always distort and go out of round, this has been a significant problem with Honda"s recent engines. This poses a difficult problem with cast in liners. Amongst the most effective liners are PTP"s EVO220 block with interference fit liners from Perfect Bore, or similar Chromoduro liners in EDL"s K2000 engine, both have been machined on the best tools but are expensive. The essential measure is to use the steel dowels and adequate stand-proud, to ensure the integrity of the fire ring. Moving the thermostat will remove the thermal stress that causes gasket failure by distortion of the head and block and gasket elastomer failure. It is important to realise that there are different modes of gasket failure, but both gasket and liner failure are and always were symptoms not causes.
The block and head in the K Series are made of the alloy LM25. The crank bearing ladder and cam carrier a derivative LM24, designed for die casting. LM25 is a very adequate metal used in the better mass produced engines today. The only two alloys which offer an advantage are A357 and A354, the latter having better heat dissipation qualities, being alloyed with copper, and A357 having a lower iron and a higher magnesium content giving a higher torsional strength. Until recently it was also alloyed with Berylium. This has now been banned as those who follow F1 will know, A357 is therefore the alloy used in F1 engines, LM25 is a very adequate second choice.
So if the design of the block and the choice of alloy used in the casting are not the cause of the problem, what was causing all this vibration and distortion that so exercised Miles at Lotus?
Crankshafts
Below is a table of crankshafts measured for dynamic unbalance " F3 forces, expressed in gram/millimetres from a number of makers manufacturing steel after market crankshafts for the engine as well as standard cast iron Rover crankshafts, as measured by Steve Smith of Vibration Free. Steve uses a machine and methods which are very much more sensitive than any used outside the in-house F1 operations. He works for a number of the best motor sport teams including F1, Cart, Indy, Le Mans and also does some of the very fine work on satellite systems. Simply, his machine and methodology achieve a sensitivity that is not common.
Crankshaft |
Initial level of unbalance gm/mm |
Final level of balance gm/mm |
||
flywheel |
nose |
flywheel |
nose |
|
steel crank make A n°1 |
773.5 |
313.8 |
17.1 |
15.1 |
The levels in the right hand columns represent the levels of balance achieved by Steve. A level of 40 gm/mm represents the required level for an engine spinning to 9500 rpm. Crank A n°1 in the table was done for me to inside the F1 specification, a required level of 26 gm/mm. It is worth noting that the cranks measured in the left-hand column came from a variety of sources both direct from their manufacturers and from tuning companies who had balanced elements individually and as an assembly, and also a number of totally standard Rover iron cranks. Below is a similar table for flywheels.
flywheel |
Initial level of unbalance gm/mm |
final gm/mm |
steel make A n°1 |
238.4 |
3.65 |
Balancing and blueprinting are relative terms, all engines; Ilmor V10"s to Rover K Series engines are balanced and blueprinted to a specified required level. This level depends upon the engines use and its maximum speed of rotation. If an engine is outside its balancing tolerance it will vibrate " like an oscillating hammer, and the faster an engine rotates the more violent the hammering. Any rotating mass " crank assembly will do this, the tolerance simply reflects a maximum limit. The graph below shows how required levels of balance are derived. The lines on the graph denote the use to which the engine will be put, the lower the line the better the engine. The vertical axis denotes the vibration a system exhibits, against engine speed on the horizontal axis.
[graph placeholder]
Point D exhibits the point that a factory balanced K Series crank is toleranced to for a 7000 rpm rev limit. Point C is the intersection with an engine speed of 9500 rpm that is required of a modified K to make this rev limit possible. This equates to a required tolerance of 40 gm/mm. Point A indicates the tolerance of the aftermarket cranks as measured to an engine speed of 7000 rpm and B the same cranks to an engine speed of 9500 rpm. In other words all the steel crankshafts are at least 10 times out of tolerance for a standard engine and more that 20 times out of tolerance for an engine with a raised rev limit. It is a similar story for the flywheels measured. Points A and B mark a tolerance that is appropriate only for agricultural diesel engines!
Now it is worth pointing out, that a tolerance represents merely an "acceptable level", and that any engine builder worth his name will realise that the tighter the tolerance the better. A badly balanced engine causes vibration, this stress within the reciprocating elements and engine block, noise and heat. All this is lost power. A recent test measured a 5 litre V8 on a dyno, then balanced and blueprinted the engine to a race tolerance, without the addition of any non OE parts, subsequently the engine was found to have gained 12 bhp on the dyno, why, because internal stresses were minimised.
The fact that some of the cranks and flywheels measured, come from engines that had been built by specialist tuners, indeed one from a car manufacturer, is nothing short of breath-taking and is the cause of all the bottom end problems that the K has been suffering. Quite simply suppliers and engine builders have been using components that are wildly outside the tolerance for a standard factory engine and exacerbating the problem by then raising the rev limit. This is why all these tuned engines are so rough when compared to a standard factory engine. They rev more freely with less advance in the mapping, lightweight flywheels and clutches, but put back-to-back, the modified engines are rough. The degree to which these engines actually see this unbalance depends upon the relative position of unbalance of flywheel and crank. Opposite and they will cancel these forces out to an extent, if they coincide they combine, and I have seen resultant bearing loads as a result of these F3 forces top 120 kgf @ 9200 rpm, this compares with a standard factory crank and flywheel measuring 6.7 kgf @ 9200 rpm.
Failures
At best these engines will be highly stressed, lose power, wear more rapidly, be noisy and will not spin up " rev - as a properly built engine working within appropriate tolerances and at worst, the bearing loads become so much as to squeeze out the bearing oil film, resulting in seizure and total failure.
A good example of the consequences is Mark Waldron"s experience with his carbon fibre turbocharged Elise, much featured in CCC. For three years he used an engine tuned to 300 bhp with a standard iron crank, and although I believe the crank"s balance was not improved to cope with the increased rev limit of 8500 rpm, which would have lost him power, the engine nonetheless was successful in carrying Mark to the championship three years running. This is great testament to the strength of the basic engine. Nonetheless last year Mark sought to build a 400 bhp engine with a 9000 rev limit, and commissioned a bespoke steel crank. Figures for this crank are listed in the table. It was similarly poor, and combined with the raised rev limit; the crank caused the engine to fail catastrophically on its first race! Putting the rods clean through the block " the same failure that has happened so often with many of these badly built and balanced engines.
Similarly MG racing have found that their 1600 Supersport WRC car had been suffering high levels of vibration causing, all manner of failures. This also had a specially commissioned steel crank. The engineer at Rover responsible for crank design suggested that the crank was measured on the standard factory balancing machine. It was again found out to be wildly out of tolerance. Now the factory balancing machine is not a particularly sensitive machine and is calibrated only to a tolerance for a mass produced engine specified to a 7000 rpm rev limit, however not only is this machine consistent it is clearly much more sensitive than the machines the aftermarket steel cranks are being balanced on.
Why Balance?
It is not my intention to discuss balancing procedure in this article, however briefly most of the balancing machines used by the aftermarket tuning companies are the old Italian CEMB and CAMM machines. These are often insensitive and poorly maintained, so much so that it is a waste of time mounting a crank to them, and completely inappropriate for a highly toleranced modern alloy engine like the K. There are also a number of modern and expensive Schenck machines in use. These are often not that sensitive either when challenged and are frequently end driven, which confuses sensitivity and residual imbalances, and causes the unequal unbalances end-to-end on a crank. This is apparent as the difference given between figures for nose and flywheel ends in the tables. However, these machines should be capable of acceptable results. The fact that they are not is due to setup, design, or methodology, I do not know which. One of the crank manufacturers has recently accepted that it has a problem with their machine, but it has taken a long time convincing them.
The fact that these engines are being built with the reciprocating elements so badly balanced, makes an absolute nonsense of any claim to blueprinting, and as I have attempted to show with the graph for required levels of eccentricity the standard crank"s tolerance is not adequate for an engine with a higher rev limit.
This then is a major issue, so what is the attitude of the tuning companies to this problem? Well I suspect that a number, including the sports cars manufacturers were blissfully unaware of the issue, the balancing machines being used are simply so insensitive that they are not reading the problem. However I have given these results to some companies who have accepted the validity of the data, and yet they have not changed their procedures. Why is this? Well I got a number of answers. Common is "that these engines are only involved in club motor sport and to take the engine building to a higher level is unnecessary and expensive." This attitude is both intellectually and procedurally totally unacceptable. The design and production engineers involved with F1 and Nascar engines with whom I have discussed the K Series are utterly appalled, as are Rover"s own design engineers, and secondly it is not expensive, a pulley, cam sprocket, pump, crank, flywheel + clutch cover costs less than £100 to balance to F1 spec. Pistons and rods more, rods because they are so difficult to balance, but it is not expensive.
The other claim I hear is that people accept the data but deny there is a problem. On those engines where the flywheel and crank combine to cause the highest bearing loads, 9000 rpm seems to be the limit beyond which failure happens, although the Lotus One Make series lost approximately 15 engines out of the 60 built when revved to just below 9000 rpm. This happened on downshifts, the engine was limited to 8000 rpm. Rather than tolerance their R500s that so often suffered failure, Caterham and their engine builders dropped the rev limit 700 rpm to 8500 rpm amongst much mutterings of narrow bearings " a solution which did not address the issue at all. Other companies propose using Steve at Vibration Free but do absolutely nothing except start making claims that there engines are well balanced when prior to an earlier version of this article getting about nothing was said about dynamic balancing at all! To date there are no currently available steel cranks for the K, with an adequate tolerance for dynamic balance at any engine speed from anyone.
There are also a number of other problems that result from a badly balanced engine. Firstly broken oil pumps. A steel pump is a useful precaution on a race engine to replace the cheap sintered original, but it"s a sticking plaster solution to the problem. The cause of failure is engine speed and an out of balance engine. Similarly with alternator problems caused by resonances, bolts working their way loose on the engine, even clutches and ring gears shattering sending shards of metal through the bell housing. All quite apart from the efficiency loss, the increased wear, and just plain simply a foul engine, but then people will never really appreciate that until they have a properly balanced engine to compare. A related issue is that of the dynamic damping provided by the front pulley. The resonances resulting from the specific rotating assembly are carefully calculated and moderated by the damper which uses a rubber with a carefully chosen modulus. Change anything, for instance the flywheel or clutch mass and the resonant frequency will change, rendering the original pulley useless. This is true for instance on the VHPD engine, where the flywheel has been changed for a lighter one, but the standard pulley retained. In such cases the modified resonant frequencies can damage not only pulleys, frequently causing them to come apart as the rubber disintegrates but it is often the cause of sintered oil pump failure. The resonant frequencies are easily calculated, in fact one of Lotus"s many arms sells a computer program to calculate them [!] and any properly engineered engine will have this done. In a well balanced engine these resonant frequencies will always be minimised.
As a final note on the subject, I have come across very few standard iron cranks that have broken in 1.8L engines despite some being revved to 9000 rpm. Those that have have all been in heavy steel bodied cars, or in German TUV tests involving standard road cars. There have been a number of VHPD cranks break, but the suspicion is always that the Tuftriding process given to those cranks is the cause of those failures. Tuftriding always runs the risk of causing the cranks to warp because of the extreme 1000° C+ temperatures of the emersion bath, one reason why Tuftriding has now been replaced as a hardening process by plasma nitriding. A standard crank and flywheel do need their balance improved to be properly toleranced to rev limits higher than the standard 6500 rpm, however the fact that some have managed higher engine speeds without failure and the steel cranks and flywheels have been the cause of so many spectacular failures, suggests strongly to me that there is no good reason to use any of the current steel cranks, particularly as all those available are not sophisticated designs or address any of the other issues such as improved big end oiling.
Counter Weights
The issue with the iron crank is that it is under-counterweighted. The confines of the compact block and the limitations of production machining have combined to produce an effective counterweight to the piston and rods that is less than ideal. All the steel cranks suffer the same problem. Determining the correct counter weighting for an engine is always a theoretical approximation depending on the engine configuration. Straight sixes, V12s, flat sixes are, for instance, perfectly balanced engines. 900 V8s are a good compromise. However remove two cylinders and you have a nightmare. V6s are compromised engines with very careful crank design and damping to make them acceptable, tamper with them at your peril. The angle on a V engine is also critical in determining the state of balance, witness the problems with increased vibration that the F1 teams have to contend with as they move from 72°V to 90° and 110°. Forces that result from the centrifugal effect of the rotating masses and the inertial forces due to the reciprocating masses are cancelled or partially compensated for by the use of counterweights however in a straight four the solution can be only partial because of engine layout. The long accepted optimum was to have effective counter weighting for 100% of the centrifugal forces (F1) due to the rotating masses, added to 50% of the axial inertia forces (F2). the balance of these latter forces is compensated for by designing adequate stiffness into the block in the cylinder axis.
The alternative is to compensate for 100% of both forces however the nature of the resultant forces is to load the engine structure in the axis of the crank. The best compromise giving the least possible loading of the block is this magic formula of 100% F1 + 50% F2. Thus it can be seen that the design and stiffness of the block and the torquing of its fasteners are a very careful calculation that comes from an assessment of the loads being imposed on the engine by the rotating and reciprocating masses as well as the forces of combustion.
A deviation of 5% from this ideal counter weighting is considered unacceptable in a high speed engine. For a while this well established rule was ignored in race engines, in order to achieve a lighter crank and hence a more responsive engine. This has now been discredited as an approach to crank design because the engine becomes so stressed that bending and hence friction losses become unacceptable. Today the most sophisticated cranks, F1 cranks, have the most carefully calculated counter weighting using heavy metal to keep mass only where it is dynamically required. Crankshaft technology has advanced enormously in just the last 3 to 4 years.
Determining the required counter weighting for an opposed crank is normally considered a simple mathematical exercise, however in motor sport the use of what is called a single piston test, where a crank is sectioned and the required counter weighting empirically measured, is used to achieve a very much more accurate figure. Some work has been done on this at Vibration Free to determine how the available K Series cranks perform. All these cranks are under-counterweighted, in the iron crank this is purely a production limitation because of the limits of production machining on the crank and the available space in the block. There is less excuse for the steel cranks, as their design moreover reveals a series of missed opportunities. Under-counter weighting in production 4 cylinder engines is common. For instance, without doing a single piston test it is impossible to be definitive, however the new Ford 2 litre Duratec has a crank only 700 g heavier than the K"s and yet piston and rod assemblies that are each 200 g heavier! It is very difficult to think that this is not a severely under-counterweighted crank and together with its antiquated block design, the engine is an unlikely candidate for performance tuning.
In the K this under-counter weighting produces a bending moment over each web in the block of just less than 1000 kg @ 9200 rpm, which is testimony to the strength and effective design of the block. I know however that Rover are looking at some very sophisticated production measures to improve this in the future.
This demonstrates how a design engineer makes choices about how loads imposed by the crank are managed within the block. In the K this loading and those imposed by combustion are carried by the long bolts, which are designed to stretch as the block distorts under load. All engines have to manage this distortion and loading, it is the design that stipulates how. This highlights another of the unfortunate practices that is currently going on within the aftermarket tuning companies: the replacement of the long bolts by thicker and stiffer material. These are designed not to stretch, under for the most part, the totally misconceived idea that the OE bolts in the K are a weakness in the engine. The original bolts because they have been so carefully designed, transfer loading throughout the engines structure in a very even way. This avoids point loading, and it is hugely successful in the engine, in fact it is one of the K"s essential design precepts. The effect of the replacing the OE bolts with stronger ones, whether or not their torquing is changed, is to stress the webs between the crank and the bolt path. Rover"s own stress analysis shows that this will lead to fatigue failure of the block. I cannot say how long that will take or what the cycle will be but, given the loading of the engine this will be the result. This is dismaying partly because there are so many engines about with these bolts now, but also because for the most part these bolts are totally unnecessary, and have come about because of a complete misconception of the engine and how it has been designed. Further, since the replacement bolts tend not at yield where they are effectively stretching they will distort the block. Unless the crank path is aligned honed, this will cause the crank to bind in its bearings, with obvious consequences for bearing wear and also frictional losses to output. There are many engines, an example being Turbo Tecnic"s 270bhp supercharged engines which use a non OE bolt which is not in yield at the 60nm the bolt is torqued down to and since the factory block has the crank path machined and honed with an OE bolt at the specified torque, in yield the path will be out of round with the new bolt. This will cause distortion of the crank path, binding of the crank and bearing crush. This happened with my supercharged engine built by Warrior " where 10mm 660B long bolts were torqued to 55nm. Despite being run in on the dyno for 4 hours, the mains totally ceased to the crank after the engine was left to stand for 4 months, eventually requiring a complete rebuild. There will be considerable power losses in such engines too.  Â
The only possible need to change these bolts would be in the cause of forced induction engines running significantly over 300 bhp, because of the very high cylinder pressures generated by turbo or supercharging. In such cases it is not enough to re-specify the bolts; a systematic re-appraisal of the whole engine structure is required. First effort must be made to remove as much stress as possible from the block. The first candidate is to redesign the crank by adding counterweight. It was with this in mind that the single piston tests were done at Vibration Free and I have in preparation a sophisticated crank heavy metalled and with significant anti-windage provision which has been conceived to significantly de-stress a 350 bhp supercharged engine to levels, excepting combustion forces, lower than a standard 118 bhp K Series engine. This crank was designed to make forced induction engines over 300 bhp possible, but the crank through a number of design features will have significant advantages for naturally aspirated engines. The block will also require substantial machining of the crank path.
Thermal Distortion
The other cause of stress that can be significantly reduced is thermal distortion by the use of ceramic coating. CTG have a new coating for aluminium heads and pistons, now being widely adopted in WRC cars, which is extremely effective. Cam Coat also have such a coating, but also offer a coating for steel valves, as well as low friction coatings for piston skirts. Balzers offer Balinit C or DLC coatings for tappets, valve stems, gudgen pins as well as titanium nitride coatings for piston rings and anti galling coatings for titanium rods and valve spring retainers. Any K Series engine will significantly benefit from these measures, but given their low cost, coating valves and pistons I regard as an absolute must, giving considerable anti-detonation and oil temp benefits as well as reducing thermal stress throughout the engine. The DLC coating for tappets not only significantly increases their life, but reduces friction at the cam lobe/tappet interface by as much as 80%, this affords similar efficiency as roller tappets but without the significant weight penalties of such set ups seen in Honda"s latest engines, or Toyota"s VVTi engine.
Summary for Lotus
So then my answer to Miles at Lotus was that the K Series is a very strong engine with a significantly more sophisticated design than almost all its competition but alone amongst these last in fully taking advantage of this to minimise weight. With suitable appreciation of the engine"s design concept, it is clear that it is possible to tune to uniquely high engine outputs, but that the engine is significantly sensitive to poor quality aftermarket components and inadequate engine building. The fact is that many of the tuned engines are significantly out of tolerance for a standard engine; truly I suspect there are not more than a dozen of the tuned engines about that would pass the factory quality control tests on the production line for a basic 1.8 litre, limited to 7000 rpm! Which is shocking! This includes the so-called the VHPD engine with its lightweight flywheel, which is not a factory engine.
Had Lotus confined their modifications to dowels, moving the thermostat, and the replacement of the uniquely light cast pistons, which are very vulnerable to engine speeds over 7500 rpm with Omega"s excellent forged pistons, balancing the bottom end to a required level suitable for 8000 rpm, they would have found the engine robust and totally reliable in their race series. Additionally they would have avoided the significant expense of steel rods and crank, which were not merely unnecessary but the cause of failure. The standard liners would also have been more than adequate in an engine of just 210 bhp. In short overwhelmingly all the problems were built into the engine by the engine builders and clearly the management of the engines was badly handled by those responsible for the Lotus One Make series, when just one call to the Rover design office would have provided all the answers. The current Senior Design manager at Powertrain LTD, who started in that position in 2000, has told me that he has never received a call from anyone involved in the One make Series!
VHPD
If that"s not bad enough, it may well be that the unfortunate experience Lotus had with this series and the VHPD engine in it"s production cars contributed to their decision to start using Toyotas 1.9 VVTi engine. The VHPD engine was particularly unfortunate, not only in the way it was specified and ran as an engine, but also in the perception of many, even at Lotus, that this was a Rover designed or in some sense approved engine. The history of the VHPD is complicated, but it had its origins in a brief as a competition engine for a one-make series that was proposed by Rover. Initially Tim Seiple at the Performance, Development and Calibration Department within Rover issued a brief specification for head flow rates, inlet manifold design, exhaust manifold design, initial cam profiles and a map, at this stage no work on the bottom end specification was done at all. Some dyno work was done under Tim Seiple on an engine that featured forged two ring pistons but an otherwise standard bottom end and a revised head valve and cam specification, that ran out to 180bhp. This was done simply to initiate the project and represented the sum total of Rover"s in house involvement. The project was then handed to Janspeed to develop as an engine for the MGF Cup Series. The project was overseen by a Rover engineer, Clive Bagnall, but at no stage was any formal certification done, or any detailed specification formulated, which would have made this a commercially viable project. The commercially available VHPD engine grew out of this original MGF Cup engine, but was entirely done outside the Rover design office, and at this stage without any input from the Rover design engineers. It was a project conceived and executed by Janspeed, Minister and PTP. The engine emerged in several variations, with differing induction systems, and maps often produced by the companies using them, i.e., Lotus, produced a map for the VHPD in the Exige and the 340 R, initially using a Gems ECU for the handful of motorsport S1 Elises, changing to an ECU from the Esprit for the 340R and Exige. This engine was beset with many problems as a result of this rather convoluted conception, and was described recently by Richard Meaden in EVO magazine as "coughing and farting at low revs, hollering in pain at high revs, with nothing in between". This is an apposite and accurate description of the so called VHPD engine; unfortunately Meaden did not attribute the engine to PTP and Janspeed, which caused more than a little irritation at the Rover Design office. Briefly, this engine will not idle or pick up cleanly from low revs because the throttle bodies are a clumsy reworking of parts done to cost by reusing KV6 throttle bodies from a Rover 800 " the butterflies are much too far away from the inlets and the mechanism to balance each inlet is crude. The cams are hopelessly mistimed, more than one degree too much advance on the inlet and the exhaust are retarded by more than one degree too much. The mapping is extremely poor, the engine running far too rich, all of which mean that the engine is well down on both power and torque and exhibits poor emissions and excessive fuel consumption. Added to which, the bottom end build is hopelessly inadequate. In every engine that I"ve knocked down, the stand-proud has stood at zero thou or less! A recipe for gasket failure! The thermostat location is standard! And they have all been built with plastic dowels! The crankshaft is not a Rover crank " it has been made to a Rover drawing by a French company, it has been tuftrided, and it is also very badly balanced as fitted to the engine. The flywheel is equally badly balanced, but is also mounted to the crank with a dowel hole far too large, which means that any balancing process is entirely wasted because the location of the flywheel to the crank can never be guaranteed. In other words, the engine coughs and farts because the induction system and cams are so badly calibrated, it screams in tortured pain since the engine is so hideously out of balance and there"s nothing in between as the engine is so badly tuned as to be well down on the torque that it should produce. The engine is a total catastrophe and should never have been sold or fitted to any car and is very largely responsible for the reputation that the K suffers. It is absolutely disowned by MG Rover and Powertrain LTD.
Federalizing the K
It has also been the cause of much speculation that the Toyota engine was chosen because the K was not federalised for sale in the US. It is certainly true that the K4 is not currently federalised and when Tony Schute asked Clive Danks three years ago, that was the answer he was given. What is not understood is that Powertrain Ltd now operates on the basis of supplying engines to customer demand, so the question that Schute should have asked was, "Can you supply a federalised K4?" There is an assumption widespread at Lotus that not only would it be prohibitively expensive but technically difficult to do this, most notably because the K does not have a knock sensor and is belt-driven; I have been told several times that in order to federalise an engine, that engine must be chain driven. Arnie Johnston, until recently CEO Lotus US, has been quoted as saying that the K is such an old design, that it is technically unfeasible to federalise it and furthermore that it will never manage Euro 4 emission standards. In fact the engine is now Euro 4 compliant and will be released in its new specification shortly, with incidentally a knock sensor. On May 8th last year, Clive Danks and Ian Fleming actually attended a meeting with Tony Schute, Jeff Grose, Paul Birch and Ian Colley with a view firstly of dealing with the perceived unreliability issues of the K, but also to discuss supplying new versions of the K to Lotus. Unfortunately, Tony Schute was called away from that meeting, and I know Clive was very frustrated in not being able to make a presentation. Subsequently, Clive thought that the deal with Toyota was a done deal, but the fact remains that the conversation about federalising the K and what that would involve never happened. I have spoken to all the design engineers and Tim Seiple, who would be responsible for the federalisation and it is quite clear that in the same way that Ford asked for the KV6 to be federalised, federalising the K would not be a problem and that there are a huge number of misapprehensions. For sure, there are no technical issues. FACT: US emissions standards do not technically require either a knock sensor or for the engine to be chain driven. The belts on the K actually have a 120,000 mile life and in the same way as for the KV6, the K4 would not be presented with any problems passing endurance tests required in the US. FACT: there would be some expense involved, but most of this would be in-vehicle work, which would be required just as much for the Toyota engine, as the K, and therefore would have to be funded by Lotus, whichever engine they chose. FACT: the K4 shares many components with the KV6, and the KV6 is now widely sold and has an extensive distribution and maintenance network in the US through Ford. I know that Toyota is selling the VVTi engine to Lotus for the exact same money as a base K series. In other words, they are selling it at a huge loss since it is a much more expensive to make with its roller bearing tappets, forged crank etc. Therefore, there may be some cost implications that favour the Toyota, but Lotus simply have not asked the questions to know how feasible a US federalised 200 bhp K series engine might have been. The other issue is the cost of the original VHPD engine which I know was an issue at Lotus. The VHPD is actually built from a standard engine bought from Rover- the total extent of Rover"s involvement- which is knocked down and then rebuilt with a number, in fact a majority of non OE parts. This is just about the most expensive way possible to buy an engine and very much more expensive than asking Rover to supply an equivalent engine! What amazes me is that the issues have never even been discussed let alone properly understood, and I continue to hear from people at Lotus that Rover are currently unable to develop K, an assertion that has no basis in fact and since Lotus have not met with Rover"s Commercial Director to ask, these assertions seem almost to be negative briefing.
BMW Connection
What has subsequently emerged from speaking with a number of people at Lotus is that Lotus had in fact been very keen to have a federalised K going back to the BMW ownership days at Rover. Mark Vinelli and Malcolm Powell tell me that an approach was made from Lotus"s highest echelons to ask whether Lotus themselves could develop the engine and federalise it for the US. No one that I can find at Powertrain or Pheonix is or was aware of this approach and so therefore it can only be speculation that Terry Payle in his inimitable style approached senior BMW figures informally with a proposal for Lotus to do this work but was rebuffed either because BMW didn"t want any competition from sporty Rovers or Rover engined Lotus"s in the US to compete with their saloons or Z3, or there was a misunderstanding about the engine involved since BMW had laid plans to replace the K with their new "common" engine in all BMWS and Rovers, this is the engine now powering the BMW 1 series. Whatever the mechanics of this misunderstanding were, no one actually charged with the commercial dealing at the then MG Rover were aware of this approach at all, it has come as a complete surprise to everyone at Powertrain LTD that anyone at Lotus made a request to do the federalising work at Lotus. Had this proposal been formally put to the commercial Director at MG Rover, with the budget I now know that Lotus spent to federalise the Toyota for the Elise, I"m told that the Elise would have had it"s 200bhp federalised K in all likelihood two years ago. All in all the handling of this engine both by way of tuning it and in commercial negotiations has been woeful, and a huge missed opportunity and all because no one sat down and talked it through properly.
Toyota Engine
The Toyota engine is now established with Lotus and one would wish this amazing company the best of luck with it in the US, given that the emission work has been done, however it seems very strange to offer the engine in an Elise here. In its favour, the Toyota engine does boast an "almost" headline grabbing 190 bhp and is very cheap for Lotus to buy. Against it though, it is a short stroke engine which consequently produces poor torque 133 lbft, only 8lbft more than the standard 118bhp k series and the Toyota has to be revved hard to get there, max torque coming in at 5800rpm as opposed to the Ks peak at just 3000rpm! What is more the Toyota only revs to 8250rpm which hardly justifies the short stroke design. I heard that Jeff Grose busied himself during the launch of the Toyota engined Exige, showing journalists, power and torque curves which he claimed reasonably equated the Toyota"s output, with the old VHPD. This exercise entirely missed the point - the VHPD"s performance is dreadful and that were it to be developed properly "by Rover" even the existing cams would give a solid 200bhp and 150lbft of torque @ 4000rpm, enough to comfortably beat the Toyota and be a much easier drive. Furthermore since the Toyota is so heavy " 127kg, dry as opposed to 82kg for a dry VHPD; - that"s a 54% increase in engine weight, the power to weight ratio of the Toyota is poor. In fact given that the new Elise 111R and Exige S2 have seen their kerb weights bloat to 860kg, even without the plethora of extras which most of these cars now seem to have [these send the kerb weight to 925kg "equivalent" to a conventional steel bodied Rover 25 !!!!!!!!!!!] this gives a power to weight ratio of 218 bhp/ton, equivalent only to the old Elise S1 160, which again was a poor non Rover engine but nonetheless had more accessible torque and therefore more grunt than the new Toyota engined cars. The new Exige is apparently quicker than the old S1 Exige, but Lotus have done an immense amount of good work to improve the new car"s suspension and it benefits from Yokohama"s A048s, so it can honestly be said that the improvement comes despite the new Toyota engine. Recent German tests in Magazin Sport Auto, pitting the S2 against a S1 with a standard VHPD engine but shod with A048s put the S1 1.7 seconds a lap faster around Hockenheim. Given Colin Chapman"s famous quote "more power makes faster on the straight, less weight makes faster everywhere" the choice of the Toyota engine not only seems to make little sense, at least in the European market but defies Lotus"s own fundamental principles. The Exige S2 has had some good reviews and everyone wants Lotus to succeed, but many who have driven the new car, including journalists who have written good reviews of the S2 are privately less than convinced about the engine. Lotus no doubt will look to boost the S2"s power to weight ratio of 218 bhp/ton past the 230 bhp/ton [242 bhp/ton claimed ] of the old S1 Exige, perhaps by supercharging however there are a number of features of the Toyota engine that mitigate against this. Firstly the engine has an induction system already biased to high revs, i.e. long duration cams and big valves and there isn"t therefore that much more potential there, certainly for better torque. Secondly the engine has an 11.5:1 compression ratio and therefore any meaningful supercharging will require a change of rod or piston which will be expensive and thirdly the engine has the bane of some new engines " cast in iron liners. These will not only limit any increase in power output without the risk of liner distortion " Honda have had just this problem with the cast in iron liners in their Civic R 2 litre engines " but they will be very expensive to replace. The Toyota"s liners are just 2.2mm thick, the Honda K20A has 2.5mm thick liners in an aluminium tower and these now have a well established reputation for going oval, they had to drop the rev limit by 500rpm on the S2000 road car it was such a problem and I"ve heard the Civic-Rs are not immune on the road either. The standard 1.8 Ks iron liners are 3.7mm thick, so it is quite reasonable to expect the new Toyota engined cars to suffer serious blow-by once they have begun to see 10 to 20,000miles including hard track use as they inevitably will in the Lotus [ unlike the Celica"s] given Honda"s experience. All in all it is difficult not to think that Lotus would not be far better off with a properly developed " by Rover this time " K series engine, more power, much better torque and more driveable, much lighter with all the benefits that that confers to handling and braking, let alone straight line performance and with much more potential to develop.
Tuning the K
The real problem with the K has been that it is the first truly optimised engine to see mass production, and very few of the tuning companies or individuals involved have had the knowledge or experience to handle it. Most of these companies were only previously experienced with the older generation of iron block engines and their techniques and practices are only appropriate for this older generation of over engineered engines. Clearly it is these practices and the general lack of adequate tolerancing that have caused the K series engine to fail so often. There is considerable evidence, however that this is not a problem now affecting just the K but also many of the other, newer generation engines from other manufacturers used in the lower motor sport series, F3, BTCC etc. But it is widely considered as a K series problem and really only as a K series problem because the Ks see a much higher level of tune " BTCC engines are limited to a modest 8500 rpm, F3 to a mere 6000 rpm, but also the sheer number of Ks around in motor sport, which dwarfs the numbers of all the other engines put together! So there are so many more to go wrong and most of them are in the hands of individuals rather than sponsored teams. In fact there are considerable problems with all of the newer generation engines, some related to poor build, some not! Clear evidence of what a competent build can achieve can be seen with the West Surrey Racing team who switched from the KV6 to the K4 in the BTCC series this year. Despite hurried development the team not only moved from midfield running to the front and winning, furthermore the BTCC Ks didn"t suffer a single engine failure all season, including the standard gaskets. There were two stops, one due to a throttle pot failure and another due to no threadlock being used on the oil pump retaining bolts causing the oil pump to work loose Compare this to the much vaunted Honda K20A in the works Honda and Dynamics teams which between them lost 8 engines to total failure. This is the engine that many foolish people replace their Ks with in their Lotus Elises. It is worth noting that the power outputs of the West Surrey team"s KV6"s andK4"s is very similar and that the dramatic improvement in the team"s performance is due entirely to the reduction in weight of about 30 kg and that in a 900kg car. Imagine then the consequences of adding 40kg to a 700 odd kilo car like the Elise by changing engine from a K to a Honda K20 or even the Toyota engine! As a footnote it is sad that Gavin Kershaw has decided that he is at the end of the road with his K series racing in the GT series when his Shollar 2.0L engine is at least 60bhp behind the 2.0L BTCC engines this year.Â
Summary
Quite simply the K is a very remarkable engine, the best four around and uniquely suited to motor sport, far more so than the heavy Japanese copies with all their over-engineering and most particularly the 2L Duratec with its archaic bearing cap design. It deserves very much more recognition for the engine that it is, however it has been badly let down by companies trying to tune it, in fact murdered! What is totally amazing is that these companies, particularly the sports car manufacturers have not gone to the Rover design engineers for any help or advice at all. This has also latterly become the case when developments of the engine were required for different markets and far too many wild assumptions have been made. This has been a huge mistake and a missed opportunity. Given proper respect and understanding it is unbeatable as a four cylinder, and is still ahead of all it"s rivals, but when tuned it must be treated with the respect and care with which it was designed. Given proper appreciation and competent building, it is an exceptional engine. With a host of new developments including the heavy metalled crank, new 2.0L versions " currently producing almost 300bhp and 190lbft of torque on a plenum [!] it seems that the best is still to come from this engine and that it will continue to considerably outperform all it"s rivals.